The Spindle-Type Cotton Harvester
Seed Cotton Handling Systems
Three methods of handling picked cotton are available, each requiring unique procedures, equipment, and harvest personnel. Each harvesting system has comparative advantages and limitations.
Basket-Based (Conventional) System
Conventional basket picker stops on the row and unloads into a boll buggy for greatest field efficiency (about 70% of time actively harvesting).
Case IH onboard module building picker unloading sequence.
Pickers with simple basket systems typically unload into a boll buggy, which then unloads into a module builder. Under good management, these pickers can spend approximately 70% of their operational time actually picking. This process requires good communications between picker and boll buggy operators. They can communicate verbally, by signaling with vehicle lights, or by routine unloading patterns to signal the boll buggy operator where the picker will need to be unloaded.
Picking Patterns
Stopping the picker on the row and pulling the boll buggy beside it within a few seconds is most efficient. The basket is then raised, unloaded and lowered, and then the picker resumes harvesting. Operators should develop picking patterns based on unloading near row ends – even if baskets are only partially full – in order to minimize field compaction from the boll buggy and tractor or making ruts when the soil is wet. Unload the basket into the wind to minimize scattering of the seed cotton on windy days.
Half-Module System
Case IH manufactures one of two available onboard packaging systems that offer nearnonstop harvesting potential. The systems eliminate module builders and boll buggies, along with their operators and tractors. This onboard rectangular module-forming (OBRMF) harvester forms modules that are 8 feet high (maximum), 8 feet wide, and 16 feet long. Each module requires a cover (fitted tarp) to prevent wind-related losses. These modules typically contain 6 to 7.5 bales of seed cotton, depending on yield, row length and operator decisions (manufacturer’s specifications indicate 4,000-12,000 pounds of seed cotton).
When operating this picker, be careful to minimize shearing of cotton from the module as it is ejected. Two modules are usually loaded for transport. When loading, carefully align the truck with each module. Always space modules at least 2 feet apart on the turn row for temporary storage; space them farther apart if necessary to meet fire insurance policy criteria. Loose cotton that is raked or piled at the base of a module will not be covered by the tarp, so it becomes wet when it rains and can wick water into the adjacent module. Also be careful loading loose cotton between two modules on the module truck. If this loose cotton is not separated at an intermediate storage site to await ginning, rainfall will soak into both modules and cause the cotton to rot.
Round Module System
The John Deere On-Board, Round-Module-Building Picker rolls a cylinder of cotton 7.5 feet wide and 7.5 feet in diameter. This picker wraps each cylinder with three layers of plastic film around its circumference just before discharging the module. The wrap practically eliminates losses from wind and movement of the modules. Each module typically holds about 3.75 bales of seed cotton. Do not place the modules closer than 4-8 inches apart to avoid interference during loading and weather damage during storage. This picker has a “surge hopper” that allows harvesting to continue while the finished module is being wrapped. Currently, each roll of plastic film will wrap 22-24 round modules (depending on manufacturer’s supply and criteria). Thus, reloading requires stopping to rethread the wrap after picking 80 or more bales of seed cotton. If the plastic wrap is damaged, you need to repair it quickly. Stop immediately if a rain shower occurs during harvesting – stop in mid-row if necessary – and wrap or discharge and cover all cotton in the harvester. There is less mixing of seed cotton with onboard module pickers. Thus, wet seed cotton concentrates in a layer on top of or around the module, likely causing quality to degrade. Flag any modules made during rainfall and stage them for immediate ginning; ask gin personnel to gin these modules as soon as possible.
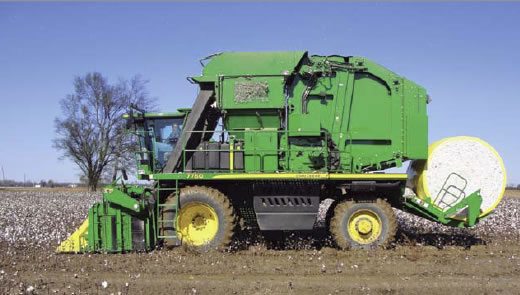
John Deere round-module-building picker carries a module before unloading while picking to the end of the row.