Irrigation Management
Irrigation Systems Overview
Key Points:
- There are many ways to deliver irrigation water to the field.
- The best system is field specific.
There are several options for delivering irrigation water. The three major categories of irrigation systems are:
- Sprinkler irrigation systems – where center pivots are the type most commonly used for cotton production;
- Surface irrigation – applying the water down the furrow from siphon tubes or poly-pipe as well as flooding an irrigation basin;
- Drip irrigation – surface or subsurface. Each of these systems is described in more detail in the following sections. Many factors determine which is best for a particular field including soil type, field slope, field geometry, and water source (well capacity or surface water).
Subsurface Drip Irrigation
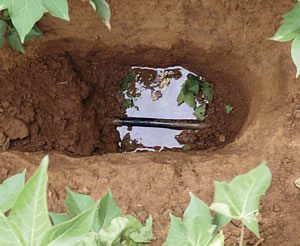
Figure 9.1 – Drip tube installed between the rows of cotton.
Subsurface drip irrigation (SDI) is proving to be an economical method of water application to agronomic row crops such as corn, peanuts and cotton. A subsurface drip irrigation system offers many advantages compared to other irrigation systems. There is less annual labor and an increased life expectancy; a dry soil surface reduces the occurrences of soil-borne diseases and helps to control weed infestations. The dry soil in furrow enhances trafficability and reduces soil compaction. There is a more efficient use of water and nutrients, and there is a significant improvement in yield and quality components.
SDI is normally defined as a “permanent” system, that is, the drip lines are not taken up every year. SDI systems must be carefully designed and installed so that they operate with proper efficiency and so that fertilizers and chemicals can be applied in a uniform and efficient manner.
Before the design of an SDI system is done, it must be determined that the intended site is suitable for SDI. These considerations include adequate water supply, acceptable water quality, and appropriate topography. Another consideration is management, which is important to all drip irrigation systems and especially important to SDI systems in which drip lines are below ground – out of sight.
The design of an SDI system is similar to the design of other drip irrigation systems, with additional consideration given to system flushing and traffic. In humid regions, topography and field layout will normally demand extra attention.
Design Criteria
1. Water Requirements:
The SDI system must be designed to deliver the required flow rate, and the water supply must be adequate to deliver the amount of water required over the growing season. The SDI system may be intended to irrigate more than one crop (rotation), in which case the crop with the highest water demand should be satisfied. The amount of water required will depend on many factors, including climate, crop, and soils.
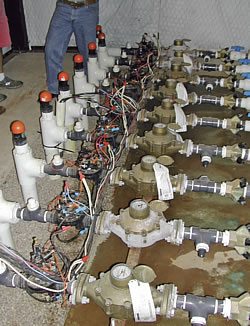
Valves controlling water delivery to different drip irrigation sections
Climate: In humid areas, the water requirement is normally lower than more arid regions due to reduced vapor pressure gradient, or driving force, for evapotranspiration. Other factors, such as temperature, sunshine and wind influence evapotranspiration. With an SDI system, evaporation from irrigation is reduced to a negligible amount in most cases, since the soil surface is not normally wetted.
Crop: The most important aspect of crop water use for SDI design is the “peak” water requirement or the amount of water that a crop uses during its highest water use period. While rain may be factored in to reduce the irrigation requirement for a season, it should not be factored in when calculating a peak use rate. This is because, even in humid regions, the probability of receiving appreciable rain in a few-day period with high dependability is low. The design flow rate calculated for crop water needs must be matched to the manufacturer-specified drip line flow rates at the recommended pressure.
Soils: The soil type into which an SDI system will be installed can impact system design. Soil characteristics such as texture, structure and layering can affect soil hydraulic characteristics such as infiltration rate and hydraulic conductivity. Drip lines will need to be more closely spaced in a sandy soil since the lateral spread of water from the drip lines will be less pronounced than in a finer textured soil. Slow emitter emission rates may be required on heavy textured soils, such as clay, so that the emission rate does not exceed the hydraulic conductivity of the soil. In general, drip line depths should be shallower in coarser textured soils and deeper in finer textured soils.
2. Management and Operation Considerations:
An essential step in the design of an SDI system is to consider how the use of the area will vary. It is not enough to design only for next year’s crop. A well-designed system should be in operation for at least 10 to 15 years, so some attempt must be made to plan for the future. Important questions that should be asked include: a) Will the same crop be grown each year or will there be a rotation of multiple crops? b) Will the entire field be planted to one crop or will it be divided into smaller areas of different crops? c) Will the different crops in a rotation employ different cropping systems? d) Is subsoiling a part of the production system? In addition, there will be system maintenance operations (e.g., acid injection, iron settling, flushing, etc.) not required or less extensive than for other types of irrigation systems. Ignoring the maintenance to save time will most likely lead to a significantly shorter life for the system.
3. Water Quality:
When designing an irrigation system, water quality concerns may include two sources of design criteria, one for the system and one for the crop. Water quality criteria for crops normally focus on leaching requirements or application concerns (foliar burning, etc.). In humid regions, where salts do not build up in the root zone, a leaching requirement is not required. Also, since SDI systems don’t wet the plant, problems resulting from the contact of irrigation water with the plant are not an issue. As a result, water quality criteria for the design of SDI systems in humid areas focuses on irrigation system concerns. Emitter clogging is the primary concern with SDI systems as with all drip systems. Water quality will dictate filtration requirements, chemical injection requirements and management of SDI systems to prevent emitter clogging.
Filtration Requirements for Subsurface Drip Irrigation
Filtration is critical in SDI systems. Since the emitters are buried, determining the location of clogged emitters is very difficult. For optimum performance, only clean (free of particulate matter) water should be pumped through drip irrigation systems. The size and type of filter required will depend on the water source and the kinds (if any) of fertilizer and chemical stock solutions to be injected. Filtration systems are placed at the headworks of the SDI system.
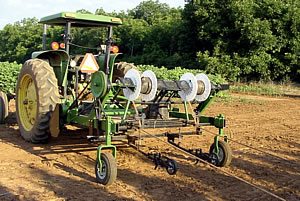
System used to install surface drip tape.
1. Media Filters: Media filters are superior for filtering surface water due to their large filter area and capacity. They can be quickly back-flushed for cleaning which can be automated. At least two media filters are needed, since during the back-flushing operation; clean water from one filter is used to remove contaminates from the other filter.
2. Screen Filters: Screen filters are used as secondary filters with surface water systems or as primary filters with well or municipal water sources. Screen filters vary in both shape and size. They may vary in size from 1 inch (for one acre or less) to 10 inches in diameter. Mesh sizes range from 40 to 200. Although some screen filters have automatic back-flush capabilities, most need to be manually flushed.
3. Disk Filters: Disk filters are used as secondary filters with surface water systems or as primary filters with well or municipal water sources. These filters contain a series of grooved plastic disks that may have an equivalent screen size ranging from 40 – 200 mesh. Disk filters have the advantage of having more surface area than screen filters and are therefore better suited for higher flow rates and are also easier to clean.
Chemical Injection for Subsurface Drip Irrigation
Chemigation refers to the application of a chemical into an irrigation system. It includes the application of chlorine, acids, fertilizers and pesticides. Because drip emitters are small, they clog easily. Along with filtration, the capability to inject chlorine and acid are important features in an SDI system, especially in humid regions for removing algae. Other benefits of chemigation are uniform and timely application of fertilizer, reduced soil compaction due to reduced traffic, and reduced labor requirements, exposure to chemicals, and environmental contamination.
The design of a chemical injection system involves the selection of the injector, both type and capacity (size). If the injection system is to be used for fertigation, the injection unit should be sized for this since injection rates for fertilizers are usually much higher than injection rates for chemicals such as liquid chlorine or acid. Two basic types of injection pumps, the Venturi injector and the metering pump, are commonly used for injecting fertilizer and other chemicals into drip irrigation systems.
Valves for SDI Systems
As with any drip irrigation system, proper selection and placement of valves is critical in an SDI system. Water flow rate and pressure throughout the SDI system should be precisely controlled to ensure efficient and timely water application. Valves play key roles in controlling pressure, flow and distribution under different conditions to optimize performance, facilitate management, and reduce maintenance requirements in SDI systems. Valves used in a complete SDI system include check valves, shut-off valves, pressure relief valves, electronic remote control valves, pressure regulators, and air/vacuum pressure regulators.
Main and Sub-Main Design
In normal irrigation design, pipe size should be specified based on economic, friction loss, and water hammer considerations. In SDI system design, pipe size may also be dictated by flushing concerns. Main and sub-mains are normally “telescoped” or reduced in size as water is discharged along the line to sub-mains or drip-line laterals, and required pipe capacity is reduced. Lateral length will determine the zoning and therefore the layout and design of sub-mains. New developments in drip-line production allow designers to extend lateral lengths to distances that were previously considered hydraulically impossible. Larger diameter drip-lines and lower flow rate emitters combine to allow lateral lengths of up to 1,320 feet in some cases. While these distances are now possible, they may not be advisable when drip-line flushing is considered. Care should be taken to properly size sub-mains where field shape varies. In these instances, each drip-line lateral may have a different length and a different total flow rate for that lateral. Sub-mains should be designed based on actual flow rates of the laterals and not on an “average” flow rate per lateral for irregularly shaped fields.
Drip-Line Design
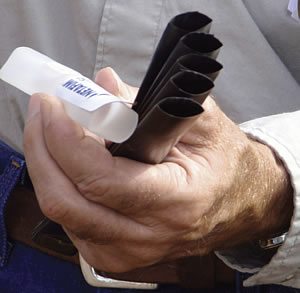
With any irrigation system, the design process starts at the plant and works “upstream.” Hydraulically speaking, this means that the first step of the design process in an SDI system is drip-line design. The design of drip-line for SDI systems consists of drip-line selection, and specification of drip-line depth and spacing. Drip-line selection will depend upon plant spacing, soil characteristics, and dripline durability and hydraulic characteristics. A minimum drip tape wall thickness of 15mil is normally specified. Discharge rates are normally expressed in gpm per 100 feet. Another consideration in drip-line selection is clogging potential. In general, higher flow rate emitters tend to clog less due to larger flow passages.
Drip-line depth should be specified in any SDI system design. Drip-line depth will depend on soil characteristics, rooting depth, and cultivation practices. In general, SDI systems are too deep to aid in germination, but in medium to heavy textured soils with a higher potential of horizontal and upward movement due to capillarity, it may be a consideration. Drip-lines should be installed below tillage depth. If deep tillage is required (at or deeper than the drip-line), it must avoid the drip-lines. Generally, the deeper the drip line, the less the system will promote weed germination. In Coastal Plain soils (with hardpan problems) optimum depth of drip-lines are between 13 to 15 inches for row crops. Without significant hardpan issues, 10 to 12 inches is a sufficient depth. Drip-line spacing, like depth, depends on soil characteristics as well as the crops to be grown. In general, coarser-textured soils will require narrower drip-line spacing than a finer-textured soil, since lateral water movement is less in coarse soils. In rotations that include a row crop, drip-line spacing is most often a multiple of row spacing.
Instrumentation and Controls
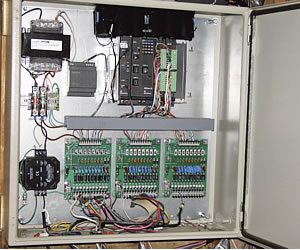
Automation of irrigation has increased in the past couple of decades. Automation can pay for itself by reducing labor requirements and by enabling more precise irrigation. Since SDI is a relatively permanent system, it lends itself to automation. Basic instrumentation starts with meters that help monitor system performance and that help diagnose potential problems. Pressure gauges are also vital in an SDI system to monitor pressure and to help diagnose problems. Low pressure and/or increased flow rates during normal operation may indicate a leak.
Irrigation control can be achieved by two general types of systems: open control loop systems and closed control loop systems. Open loop systems do not incorporate feedback and amounts and timing of irrigation are pre-determined by the operator. This type of system is usually a simple irrigation controller operated with a clock. In general, these controllers initiate irrigations at preset times and control the duration of irrigation by activating solenoid control valves that serve zones. The controllers vary in the number of valves that can be controlled, the number of valves that can be simultaneously held open, the number of separate irrigation programs available, and the number of start times available for each program. These controllers are not normally set to operate with feedback, although most offer a rain switch that terminates irrigation during precipitation events.
Since humid areas, by definition, have appreciable rainfall, soil moisture may change unpredictably, and therefore make it difficult to schedule irrigations. As such, a closed looped system offers many advantages. Automation of irrigation using feedback can prevent leaching of chemicals, and reduce pumping costs, by only allowing irrigation when the crop needs it. Many different systems for automating irrigation scheduling are available. These systems can be divided broadly into two groups: systems that infer crop-water stress using soil-water content information and those that estimate crop evapotranspiration (ETc) or crop-water use.
Surface Drip Irrigation
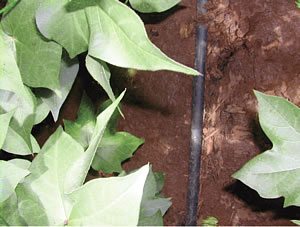
Figure 9.2 – Surface drip tape under a cotton plant.
For many years, surface drip irrigation has been used to irrigate high-value vegetable crops. In recent years, surface drip of row crops has been increasing throughout the United States. Surface drip irrigation can precisely deliver water and nutrients to the crop root zone. Surface drip irrigation systems save water by only wetting a small area of the overall soil surface, thus reducing evaporation. Additional advantages for surface drip irrigation include low application rates, precise water placement, and low operating pressures. Drip irrigation can also be used in irregularly shaped fields to maximize the irrigated acreage. Disadvantages of surface drip irrigation include the initial cost of the system, specialized equipment to install and remove tubing, and the annual system component replacement. Without proper care, some irrigation system components can be damaged with machinery. Additionally, rodents and insects can create additional maintenance problems by chewing holes in the plastic tubing.
Surface Drip Irrigation Design
A typical surface drip irrigation system would consist of a pumping plant, pressure regulation, a filtration system, and a distribution system divided into zones delivering water to the drip tubing. A major consideration in design of surface drip irrigation systems is in the drip tubing lateral spacing. Typical lateral spacing for row crop production is for either 1) every row or 2) alternative row middles (see Figure 9.3). In previous research with traditional row crops grown in the humid southeast and other more semi-arid regions of the U.S., no significant yield differences were observed between the two lateral spacings. An advantage of alternative row spacing is the reduction in tubing cost and the ease of tubing removal.
For row crop operations, the drip irrigation emitters are usually embedded into the drip tubing. The emitter spacing on the drip tubing varies but are typically spaced from 12 to 24 inches apart. Emitter spacing is determined by one or any combination of field length, field/zone size, or water capacity.
In high-value crops, surface drip laterals are typically replaced with each crop. In some row crop production systems, annual tape replacement may be cost-prohibitive while other cropping systems may be quite cost-effective. Some researchers and manufacturers have developed methods to retrieve the drip tape after crop harvest and methods to repair damaged tape. If the cropping system is using strip tillage and GPS systems for planting operations, the tubing may be used for several years before retrieval and replacement are needed.
Shallow SubSurface Drip Irrigation (S3DI)
More recently, some researchers have started using shallow subsurface drip irrigation (S3DI). The S3DI is basically surface drip irrigation buried 2-4 inches into the soil in alternate row middles. This is much shallower than sub-subsurface drip irrigation (SDI), but can reduce the damage from rodents and insects.
System Costs and Expenses
Cost for surface drip and S3DI are similar and much less expensive than deeply buried subsurface drip systems. For instance, both surface and S3DI systems can be installed for about $250 to $350/acre infield expenses. This cost includes manual filtration, pressure regulation, tubing, fittings, valves and infield mainline. This expense does not include equipment, labor, or water conveyance from water source to the field. These costs assume clean well water, smaller rectangular fields, and field lengths less than 700 feet. With proper management these systems can be maintained for 3 to 5 years depending on crop rotation.
Figure 9.3 – Surface drip irrigation configurations.
Deep SDI installation expenses can range from $1,100 to $2,400 depending on water quality and level of electronic control. These systems have life spans much longer (15 to 20 years) than either surface drip or S3DI and, therefore, need higher-quality filtration methods and flush systems. Aside from tubing, the major expenses for SDI are the required filtration and flush systems. Filtration can range from inexpensive manual to expensive electronic flush systems. These SDI systems need both input and flush mainline along with the associated valves and fittings. Installation will require heavier equipment and more labor.
Center Pivots
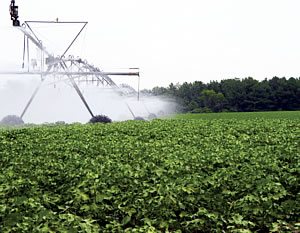
Figure 9.4 – A center pivot equipped with drop lines.
Center pivot sprinkler irrigation systems are among the most popular mechanical-move systems for applying irrigation water to field crops like cotton, and are used on over half of the sprinkler-irrigated area in the U.S. The basic design concept has been improved and refined, but remains very similar to the original system invented and patented by Frank Zybach in 1948 and 1952, respectively. Because center pivot systems have low labor requirements, apply water very efficiently, can operate unattended for long periods, and now are being automated, they have proven to be very popular, especially in the Southeast U.S. Since the late 1970s, the use of such systems has grown rapidly. Center pivot systems feature a water supply main-line or lateral that rotates about a fixed point (the center “pivot” point). The galvanized steel or aluminum lateral is supported by a series of “towers” (Figure 9.4) which propel the lateral around in a circular fashion by rubber-tired wheels driven by electric or hydraulic motors mounted on each tower. The towers support the lateral at a height such that the clearance between ground and lateral support trussing is about 10 feet to allow for ample space above most crops.
Hoffman, et al. (2007) and Keller and Bliesner (1990) note that center pivot systems have many advantages over other irrigation application methods, including:
- Potential for automated operation.
- Simplified water delivery.
- Ability to apply small irrigation depths.
- Very high application uniformity.
- Ability to improve irrigation management.
- Ability to apply agri-chemicals (chemigation).
- Ability to activate surface-applied agri-chemicals.
- Little annual setup required.
Disadvantages of center pivot systems include:
- Relatively high initial cost.
- High application rates at outer end of lateral (causing runoff).
- Relatively high pipe-friction losses.
- Circular pattern not matching square fields (leaving dry corners).
- Topographic changes causing potential operating pressure variations.
Center Pivot Design Considerations
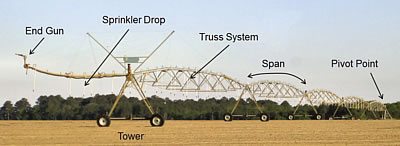
Figure 9.5 – Components of a typical center pivot irrigation system.
A typical center pivot irrigation system layout and components would include (as shown in Figure 9.5) the pivot point, control panel (user interface), spans between towers, tower drive wheels, truss system supporting the water supply lateral, sprinklers, and often an end gun (with or without an end gun booster pump). For most electric systems, a oneminute timer is used to control the “walk” (i.e., travel) speed of the end tower. The speed of the end tower around the circle controls the depth of application (assuming a constant water supply to the pivot point). A 50% timer setting would correspond to the end tower moving for 30 seconds and then remaining stationary for 30 seconds, since the end tower drive motor is a constant velocity design. Thus, the maximum travel (or “walk”) speed of the center pivot system would be when the timer is set to 100%. All interior towers have switches that energize the respective tower drive motor to start that tower walking whenever the next tower has walked ahead such that the two towers are mis-aligned. Once re-aligned, the switches stop the drive motor.
System Dimensions
The lateral spans range in length from 100 to 200 feet with a typical pipe diameter of 65/8 inch (other diameters are offered). Overall center pivot lateral lengths can range from as small as 250 feet to as long as 2,000 feet. Center pivot design professionals will often incorporate various span lengths to maximize the irrigated area of a field. Sprinklers attach to the lateral spans by way of threaded outlets, either directly to the outlet or by way of drop tubes/hoses. End guns at the end of a lateral are often used to increase the wetted area of a field as this large-volume sprinkler throws water a long distance (often aided by a booster pump).
The entire lateral is usually supplied with sprinkler outlets spaced equally along the pipe. Center pivot manufacturers offer a number of outlet spacings with 30-inch spacing common today. This close spacing allows the design professional to configure the optimal combination of sprinkler type, nozzle size, and spacing. In general, because the outer end of the lateral rotates at a higher speed than the inner span, the application rate per sprinkler will be greater at the end of the lateral than near the pivot point to achieve uniform application depth from end to end.
Sprinklers
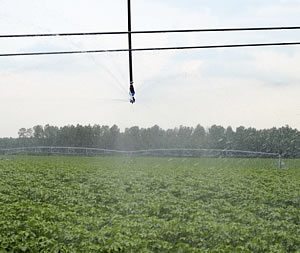
Sprinklers are the devices that actually deliver the water to the plant and/ or soil. The purpose of a sprinkler is to take water from the source (such as the pivot lateral) and distribute the water uniformly over an area in droplet form. In order to cover a large area, a sprinkler must throw water a considerable distance. A properly designed sprinkler “package” will take many factors into account including water supply, soil, crop, topography, and atmospheric conditions. High pressure, impact-type sprinklers, as well as low-pressure, spray-type sprinklers, are used on center pivot systems. Regardless of type of sprinkler, the system should be designed, as close as practical, to meet the crop water requirements for the crop and area irrigated.
Spray-type sprinklers (referred to as spray nozzles) require considerably less pressure, and thus energy, than impact sprinklers. Often spray nozzles are installed at the end of drop tubes/hoses to release water closer to the crop canopy to reduce wind and evaporative losses. However, spray nozzles have a smaller wetted diameter which causes very high application rates at the outer end of the lateral. In “heavier” soils this often leads to application rates that exceed the soil infiltration rate, causing runoff. Impact sprinklers have large nozzles giving a large wetted diameter which results in lower application rates.
Sprinkler manufacturers today offer an extensive array of spray-type sprinklers along with a few models of impact-type sprinklers. There are spray nozzles available today that have water impact plates that rotate, spin, wobble, or remain fixed to give various water application patterns to meet most conditions. Impact sprinklers come primarily in two formats – low-angle water trajectory and high-angle water trajectory. For a sprinkler package design, the irrigator will be given a “timer chart” that will indicate the application depth (usually in inches) for various timer percent settings. For example, a chart might indicate that the irrigator select 22% speed to achieve 0.5 inch application depth.
Irrigation Water Delivery
Irrigation water (surface water or groundwater) is usually supplied to center pivot systems through power take-off (PTO), engine, or electric motor powered pumps. Pumps may supply a single center pivot or may supply multiple center pivot systems. Water for center pivot systems is usually not routed through a filtration system. Flow rates to center pivot systems range from as low as 200 gallons per minute (GPM) to well over 1,000 GPM. Remember that water for irrigation is needed most when water supplies are at their lowest level. Water sources should, therefore, be adequate to supply water during extended dry periods. The required water supply flow rate for a center pivot can be calculated using the following formula:
Where:
Example:
Q = (453 x 72 x 1.25) ÷ 3 x 20 = 680 GPM.
Chemigation
Chemigation refers to the application of a chemical into or through an irrigation system. It includes the application of fertilizers, acids, chlorine and pesticides. Chemigation can save time, reduce labor requirements, and conserve energy and materials. Chemigation is beneficial, however, only to the extent that the irrigation system is adequately designed, fully functional and properly managed. In many situations, chemigation is as good or better than conventional application methods. Conventional application is still preferred or required, however, for some materials. Never inject any material that is not labeled and recommended for the crop and for injection through the system. Always follow label directions.
There are a number of advantages to using chemigation, including:
- Uniform Application.
- Timely Application.
- Reduced Application Costs.
- Improved Management.
- Reduced Soil Compaction.
- Reduced Exposure to Chemicals.
- Reduced Environmental Contamination.
However, to properly employ chemigation with a center pivot irrigation system, an irrigator must consider a number of safety and performance issues. In terms of safety, the irrigator must note that the pumping plant and the chemical injection pump should be interlocked, there should be proper check and vacuum relief valves (anti-siphon devices) installed, a pressure switch should be electrically interlocked with the safety panel on the irrigation system, plus other state-specific safety issues to be followed.
Two basic types of injection methods — the Venturi and the metering pump — are commonly used for injecting fertilizer and other chemicals into irrigation systems. The irrigator must determine the desired injection rate using area, chemical solution volume, and time and then calibrate the injection pump to put out the desired rate.
Control Panels/User Interfaces
The control panel is the user interface for the center pivot irrigation system. Control panel technology spans the range from very basic to very advanced. The primary functions of the control panel are to energize the system, select forward or reverse travel direction, and select travel speed by the percent timer setting. The entry-level basic control panels from center pivot manufacturers provide those functions and little else. As the control panel type moves toward the advanced end of the spectrum, more features are added to the package, including auto-reverse, auto-stop, digital displays, end gun controls, pivot angle, auxiliary controls, auto-speed, programming capabilities, touch screen controls, and remote monitoring and control.
Surface Irrigation (Flood/Furrow)
Surface irrigation is the oldest and most common form of irrigation (NRCS 2008). Surface irrigation is a broad term applied to irrigation practices through which water is applied to the soil surface and flows gravimetrically across the soil surface.
Field Geometry
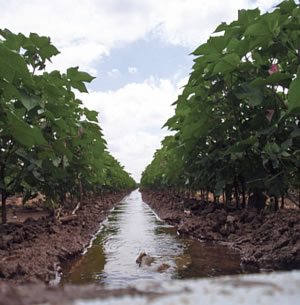
Figure 9.6 – Furrow irrigation in progress.
The field in which surface irrigation will be applied must have a positive and continuous grade to facilitate water movement across the field and to prevent water retention (University of Arkansas, 2006). In order to facilitate surface irrigation, many producers perform earthmoving operations in order to gain a positive and continuous grade utilizing equipment supplied with real-time kinematic (RTK) global positioning systems (GPS). Grades should be a minimum of 0.1% and no more than 0.5%. Grades between 0.15% and 0.3% are considered optimum (University of Arkansas, 2006). Cotton growers typically plant on beds which run from the highest elevation point in the field to the lowest elevation point. Once the crop is established, irrigation water is typically introduced to the field through a pipe system from which irrigation water runs gravimetrically down the furrows to the end of the row. To a lesser extent, growers will plant cotton flat on precision-graded fields, introduce irrigation water at a central point, and allow it to flow freely across a given field.
Row length must also be considered when using surface irrigation. Generally speaking, rows 1,320 feet or less in length are more desirable than longer rows. Excessive row length can lead to problems with soil saturation where irrigation water enters the field, whereas the ends of the rows may have yet to be watered or have only received minimal amounts of irrigation water. Irrigation should be applied for a maximum of 10–12 hours, depending on soil texture, in order to prevent water logging near the point of water introduction (University of Arkansas, 2006). If issues arise with water logging at one end of the field and dry soil at the other, growers should consider reducing the number or rows being watered at one time and/or reduce the length of irrigation runs.
Water Source
Water used for surface irrigation may come from a variety of sources. In some cases, water is extracted from aquifers using wells equipped with electric or engine-driven pumping systems. However, surface irrigation water may also be extracted from rivers, lakes, or reservoirs. In some areas of the Cotton Belt, rainfall or melted snowfall is held in impoundments until it is needed for irrigation. Irrigation water used in the siphon tube irrigation system is held in earthen ditches. In some cases, these ditches are lined with concrete or plastic in order to limit water loss through the soil (Sansone, et al., 2012).
Regardless of water source, water quality must be considered when being used for irrigation. Increased salinity of irrigation water is not an uncommon occurrence. Increased salinity in irrigation water typically leads to increased concentration of salts within the plant’s root zone (NRCS 2008). In addition, water obtained from aquifers in some areas is high in calcium. Water high in calcium that is used for irrigation can have a similar effect as applying low rates of calcium carbonate, or agricultural limestone, to the soil.
Irrigation Water Delivery
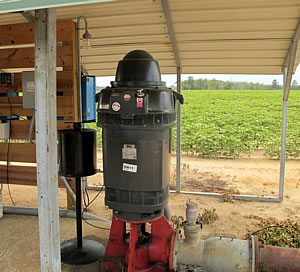
As mentioned previously, irrigation water is typically delivered to a given irrigation riser through power take-off-driven, engine, or electric powered pumps. Although engine-driven pumps have been standard for some time, some producers choose to use electric pumps. Electric pumps are not standalone units as they must be located in an area where electricity is available. In some areas, cost for use of electric pumps for irrigation is elevated during certain times of the day when general electric demand is at peak use. In order to avoid increased costs, growers should plan irrigation applications around these times. Irrigation water is typically introduced from a single point on fields that are precision graded and planted flat. Water is supplied to the point of entry through a pumping system, and water is allowed to flow freely across a given field once these entry valves are opened.
The Siphon Tube System
In most cases, cotton will be planted on beds, and water will be applied to the furrows that are adjacent to each bed. There are a number of ways that water is directed into these furrows. The siphon tube system consists of an aluminum or plastic pipe that is laid over the bank of an open ditch as described above. One end of this tube is submerged in the ditch with the other directed into the furrow that is to be irrigated. Water flows into the submerged end of the tube and is siphoned over the bank and into the furrow. Flow rate is controlled by the diameter of the tube and the elevation difference between the water surface in the ditch and the end of the outlet tube (Smathers, et al., 1995). Flow rate tends to be very uniform using siphon tubes; however, trash screening devices must be utilized to prevent trash within the irrigation ditch from clogging the siphon tubes.
Pipe Systems
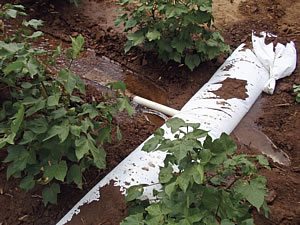
Pipe systems are very common in surface irrigation systems. Flow rate requirements for pipe systems are approximately 10 gallons per minute per irrigated acre (University of Arkansas, 2006). Irrigation water is supplied to a point of introduction; however, rigid pipe or flexible tubing is attached to the irrigation riser and are used to distribute irrigation water across a large number of rows. Once the pipes are connected to the riser, they run perpendicular to the rows. Gated pipe systems typically use PVC or aluminum pipe with rectangular, adjustable outlets used to control irrigation flow rate. Although rigid, gated pipe systems can be reused from year to year they are becoming less common. Rigid pipe systems cannot be crossed with equipment when conducting field operations, which leads to decreased efficiency and increased labor costs.
Poly Pipe Systems
Flexible pipe (henceforth referred to as poly pipe) systems are becoming increasingly popular. Poly pipe is attached to an irrigation riser and runs perpendicular to the rows similar to gated pipe. However, holes are punched into the poly pipe manually and, once holes are punched, flow rate can be increased but not decreased. Holes may be blocked if irrigation is not needed in a given row through the use of plugs. Poly pipe is available in several diameters and thickness levels. Thickness of poly pipe will dictate durability with thinner pipe (i.e., 6 mil) being less durable than thick pipe (i.e., 15 mil). As pipe thickness increases, pressure can be increased as well. Generally, pressure should not exceed 3 PSI when using poly pipe. When not in use, poly pipe will lay somewhat flat with some water remaining in the pipe. However, if equipment operators exercise caution, they can cross poly pipe when not in use without damaging it. Poly pipe typically comes in 1,320-foot rolls and, unlike rigid pipe systems, is used for one growing season only. Poly pipe is generally collected at the end of the growing season and recycled.
Irrigation Water Quality
Water quality is an important consideration in irrigation practices because of the effects on crop and soil. Irrigation water of high salt content could harm crops and induce soil degradation. Crop tolerance to salt differs significantly. For instance, cotton could maintain its maximum yield potential in a soil with electrical conductivity of 7.7 dS/m, while corn would only reach 50% of its yield potential under a similar condition. Likewise, the maximum chloride concentration without yield loss are 2,625 and 525 mg/L for cotton and corn, respectively.
Although water quality does not present serious challenges to cotton irrigation in many areas of the humid U.S., routine water quality assessment is still highly encouraged, particularly in drip irrigation systems. Emitter clogging is often a function of water quality and affects the uniformity of water distribution and irrigation efficiency. Emitters could be clogged by physical (e.g., sand and silt), chemical (e.g., salts and metals), and biological (e.g., algae and bacteria) materials. Simple irrigation water quality indicators include electrical conductivity (EC, mmhos/cm or dS/m), sodium adsorption ratio (SAR), total dissolved salts (TDS, mg/L), and bacterial counts (no./ml). Irrigation water of > 100 mg/L suspended solids, > 2,000 mg/L dissolved solids, > 50,000 bacteria (number/ml), and pH > 8.0 could increase the chances of emitter clogging.