Stripper Harvester
Stripper Harvester Preparation
Row Unit Maintenance and Adjustment
Proper row unit maintenance and adjustment are critical to maximizing harvest efficiency and preserving fiber quality. Several crop conditions play a large role in determining correct machine settings, such as the level of defoliation, stalk diameter, plant height and width, and stalk and branch moisture content (brittleness). “Stripping aggressiveness” describes the duration and intensity of the harvesting action applied to the plants by the row units.
Aggressive Harvesting
Aggressiveness directly influences the amount of seed cotton and foreign material harvested. The more aggressive the harvesting action, the higher the probability is to harvest more foreign material and generate bark. You need to adjust stripper row units to the correct level of stripping aggressiveness with goal of harvesting the least foreign material and causing the least seed cotton field losses. Four main factors influence stripping aggressiveness:
- Configuration and sequence of brushes and bats on stripping rolls
- Stripper roll spacing
- Combing pan spacing
- Machine travel speed
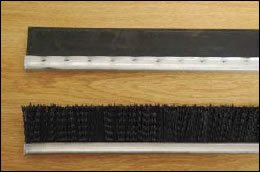
Close-up image of a new bat (top) and brush (bottom) used on stripper rolls.
Stripper Roll Configuration
Manufacturers configure stripper rolls with three brushes (2 inches wide by 40 inches long, crimped nylon bristle brush) and three bats (2 inches wide by 40 inches long, reinforced rubber strips). Brush-bats are un-crimped nylon bristle strip brushes and reduce stripping aggressiveness compared to conventional brushes. Brush bats are available commercially as replacement components. Bats with two-ply thickness are most commonly used on stripping rolls, but one-ply bats are available on new machines and as replacement components. One-ply bats help reduce stripping aggressiveness due to their reduced stiffness.
Using fewer bats per stripper roll reduces the amount of foreign material harvested. Research showed that using a stripper roll configuration with one bat and five brushes reduced the total foreign matter content of stripped cotton (Brashears, 1992). Additionally, as stalks and branches become brittle late in the season after freezing weather, reducing the width of bats by 0.75 to 1 inch can reduce stick content by as much as 40% with minimal effect on harvest efficiency (Brashears, 1992; Supak et al., 1992).
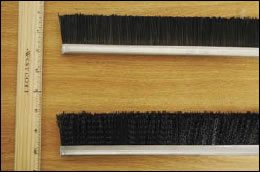
Image of brush-bat (uncrimped nylon bristle brush, top) and conventional brush (bottom).
Stripper Roll Timing
Timing of stripper rolls using the conventional three-brush/three-bat or one-bat/five-brush configurations should be brush-to-bat to help reduce stripping aggressiveness. Late-season stripper roll configurations using three narrow bats with three brushes should be timed brush-to-brush.
Stripper Roll Spacing
Stripper roll spacing – measured as the distance between adjacent bats or brushes turned to their inward- most position – should be as wide as possible without increasing field losses. Wider spacing between stripper rolls reduces the amount of foreign material collected and the potential for bark (Wanjura and Brashears, 1983; Brashears, 1986).
Adjust initial spacing between stripper rolls based on typical stalk diameter (generally 0.25- 0.75 inch), and readjust the spacing as crop conditions change. The spacing of combing pans located below stripper rolls should also be checked to make sure seed cotton is not able to fall out of the row unit and plants are allowed to pass through freely. It is generally recommended to increase the spacing of combs at the front of the unit by approximately 1/4 inch compared to comb spacing at the rear of the unit.
Monitor the condition of bats and brushes frequently and replace worn components to maintain acceptable harvest efficiency. Excessively worn bats or brushes may break off stripper rolls and become a contaminant in baled lint if allowed to pass through the gin.
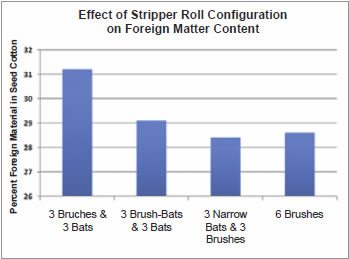
Air System Configuration and Adjustment
The pneumatic conveyance system used on stripper harvesters serves three critical functions:
- Conveying harvested seed cotton from the header to the storage basket
- Separating green bolls and heavy foreign material from harvested seed cotton
- Distributing seed cotton uniformly across the width of the conveying duct before the onboard field cleaner
A harvester uses the force of gravity to separate green bolls and heavy trash at the lower and upper ends of the conveying duct. After seed cotton exits the header cross auger, high-velocity air from the main fan pulls it through the conveying duct. The position of a door on the rear side of the duct regulates the force of the air. When the door is open, the air stream is less forceful, which provides better separation of green bolls and heavy trash. When the door is closed, all of the seed cotton, green bolls, and foreign material is pulled into the conveying duct and carried to the upper section.
A separation system at the top of the conveying duct provides a second opportunity for removing green bolls and other foreign material. A plate at the top of the air duct can be adjusted to allow more green bolls and other foreign material to settle out of the air stream and onto a chute that discharges the removed material to the side of the machine. The seed cotton remaining in the air stream is directed into the onboard field cleaner or into the basket. Uniform distribution of the seed cotton across the upper section of the conveying duct requires proper adjustment of the front and side tabs on the high-velocity air nozzle and factory-installed vanes that direct airflow across the inside of the duct.
Field Cleaner Maintenance and Adjustment
Modified stripper roll configuration with one bat and five brushes per stripper roll timed brush to bat (Brashears, 1992).
Conventional configuration of three bats (red) and three brushes on stripper rolls (rolls timed brush-to-bat).
Recommended initial stripper roll spacing.
New bat (top) and worn bat (bottom).
Cotton strippers produced since the late 1980s have included onboard field cleaners to help remove foreign material from stripped seed cotton. Field cleaners used on modern stripper harvesters are similar to two-saw stick machines used in cotton gin seed cotton cleaning systems. Field cleaners can remove approximately 50-60% of the initial foreign matter content in stripped seed cotton.
Cotton strippers produced since the late 1980s have included onboard field cleaners to help remove foreign material from stripped seed cotton. Field cleaners used on modern stripper harvesters are similar to two-saw stick machines used in cotton gin seed cotton cleaning systems. Field cleaners can remove approximately 50-60% of the initial foreign matter content in stripped seed cotton.=–> Seed cotton containing approximately 30-35% foreign material is fed to the machine through the pneumatic conveying duct where wads of seed cotton are dispersed by the feeder cylinder and fed onto the primary cleaning cylinder.
Channel-type saws affixed to the surface of the cleaning cylinder grab the seed cotton and pull it over grid bars located around the outside of the saw cylinder. Large foreign material (such as sticks and burrs) and some seed cotton are removed through centrifugal force as the cotton is pulled across the grid bars. The material rejected by the primary cleaning cylinder is fed onto the reclaiming cylinder and pulled over a second set of grid bars where mostly large foreign material and small amounts of seed cotton are removed through centrifugal force. Seed cotton on the primary and reclaiming saw is removed by the doffing brush at the back of the machine and discharged into an air stream leading to the harvester basket.
Factors that Influence Field Cleaner Performance
Several factors affect the seed cotton rejection and cleaning performance of field cleaners: loading rate, seed cotton moisture content, initial foreign matter content, saw-to-grid bar clearance, saw condition, doffer brush condition, and belt tension. You can influence all of these factors to some degree while operating a stripper.
Feed Rates
Research on field cleaners and similar stick machines used in ginning has shown that excessive processing rates decrease cleaning efficiency and increase loss of good seed cotton (Baker et al., 1982; Kirk et al., 1970). Previous research indicates that the optimum feed rate of these machines is in the range of 2-2.5 bales per hour per foot of width (Baker et al., 1994; Wanjura et al., 2009). When operating a cotton stripper, be careful not to overload field cleaners by excessive harvest speeds, especially with six-row-wide and eight-row-wide headers.
Moisture Content
Monitor seed cotton moisture content at harvest, especially when using field cleaners to avoid damaging fiber quality. Under high-moisture-content conditions, field cleaners can cause seed cotton to have a “rope-like” appearance that reduces the gin’s ability to efficiently clean the cotton. It also tends to cause excessive fiber breakage at the gin stand.
Preharvest Crop Management
Proper preharvest crop management will reduce the amount of excess plant material the harvester must handle. Specifically, timing of irrigation termination and harvest-aid application will help defoliate and desiccate the crop. Also, proper preharvest maintenance on field cleaners will help improve the removal of foreign material from harvested seed cotton. During preharvest field cleaner maintenance, check and adjust saw-to-grid bar clearances, replace worn saws on primary and reclaiming saws, replace worn doffer brushes, and check for proper drive belt tensions.
Saw-to-Grid Bar Clearances
Generally, wider saw-to-grid bar clearances reduce the amount of foreign material removed, as well as the amount of seed cotton rejected by the machine. On the other hand, tighter clearances increase foreign matter removal and seed cotton rejection. Clearance settings for the two upper grid bars and the lay-down bar on the primary saw are 5/8 inch. All other saw-to-grid bar clearances are set at 1/2 inch. Check saw-to-grid bar clearances daily and adjust as needed.
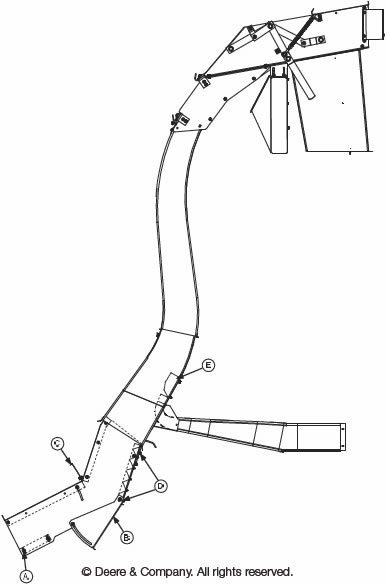
Schematic of main cotton conveying duct used on John Deere 7460 stripper harvesters (Courtesy of John Deere): A – Lower Front Separation Duct Panel; B – Lower Separation Duct Door; C – Door; D – Separator Angles; and E – Vanes.
Field cleaner machine used onboard John Deere 7460 stripper harvesters (Courtesy of John Deere):
A – Cleaner Bypass Lever;
B – Feeder;
C – Feeder Control Bar;
D – Upper Saw Drum;
E – Upper Grid Bars;
F – Lower Saw Drum;
G – Saw Brush;
H – Secondary
Reclamation Brush;
I – Lower Grid Bars;
J – Trash Auger;
K – Fan;
L – Doffer (12-Brush);
M – Brushes (Doffer);
N – Front Duct;
O – Rear Duct; and
P – Basket.