Pioneers of Progress
Agriculture
reduced pesticide applications by
1/2
increased water
use efficiency by
80%
Produced
More Fiber
without expanding
acreage
Since it was founded in 1970 through to the present day, the programs of Cotton Incorporated help the cotton industry realize its commitment to sustainable practices.
From an agricultural perspective, cotton is a commodity crop most widely known as an ingredient fiber in apparel and home textiles. Today, the global value of cotton fiber exceeds $6 billion per year. But cotton has uses and value beyond fiber in the form of cottonseed oil and meal, as well as other plant by-products, which add $1 billion annually. In many parts of the world, cotton is an economic essential: a cash crop that can thrive in hostile environments where food crops cannot flourish. Here in the United States, cotton production and processing employ more than 200,000 people, with an aggregate influence of $35 million on the gross domestic product.
Over the past 40 years, the work of the company’s Agricultural & Environmental Research Division has been instrumental in improving grower efficiency—from collaborating on the development of better harvesting systems in the 1970s, to its role as a facilitator for scientists mapping the cotton genome today.
Every year, Cotton Incorporated supervises an average of 500 research projects, 400 of which are in agriculture. Most of these projects are focused specifically on optimizing efficiencies: decreasing inputs of fertilizer, pesticides and water and identifying optimal soil conservation management practices. These efforts have led to cotton growers’ reducing the number of pesticide applications by half; increasing irrigation water use efficiency by 80%; and producing substantially greater amounts of fiber, without expanding acreage.
The environmental benefits are enhanced and validated by the transparency of grower practices. Cotton grown in the United States is among the most highly regulated in the world, requiring meticulous record keeping and reporting of chemical usage to the U.S. Environmental Protection Agency, the U.S. Food and Drug Administration, and governing bodies at the regional and state levels. The U.S. Department of Agriculture (USDA) and associated agencies, including the Economic Research Service (ERS), the Agricultural Research Service (ARS), the National Agricultural Statistics Service (NASS) and the Natural Resource Conservation Service (NRCS), also collect information on grower practices by conducting surveys on an ongoing basis and provide valuable resources and support for the implementation of conservation practices.
In addition, U.S. cotton growers conscientiously embrace any means to do their job better, from investing a share of their earnings to fund the activities of Cotton Incorporated, to their voluntary participation in studies to develop meaningful measures of environmental performance, which are key to establishing accurate benchmarks for cotton’s environmental progress and to directing research where it will be most effective.
Module Builder Technology
Then
Until the mid-1940s, cotton was mostly picked by hand. Open trailers moved the harvested bolls from the field to the gin.
NOW
New machines from Case IH and John Deere both pick the cotton and form the modules on the harvester.
One of the earliest environmentally themed projects for Cotton Incorporated was the evolution of the cotton harvest system. Until the mid-1940s, cotton was mostly picked by hand. Open trailers moved the harvested bolls from the field to the gin. When mechanical harvesting was introduced, the picking process accelerated, but ginning was slower to adapt. Farmers had to store the harvested cotton in trailers and would be forced to stop harvesting if the gin had not processed all their cotton when all the trailers were full.
Soon after its formation, Cotton Incorporated began working with Texas A&M University on a module building system, which enabled harvested cotton to be compacted and stored as a very large trapezoidal bale, 7.5 feet wide, 32 feet long and 11 feet high. These modules could stay in the field, covered by waterproof tarps, until the gin was ready to receive the harvested cotton.
Developers also worked on specialized haulers to move the modules from the field to the gin. Trucks were outfitted with tilted beds of parallel rows of conveyor chains that could load or unload the module in sync with the truck’s speed. With these enhancements, the trucks could move modules at higher speeds for longer distances.
At the ginning stage, it quickly became apparent that the traditional system used to suction loose cotton would not be effective with the compressed modules. Developers created new systems that conveyed the entire module into a feeder that rapidly separated the cotton back into individual tuffs. Because of the significant increase in efficiency, the module builder, transporter and feeder combination was quickly adopted wherever cotton was mechanically harvested.
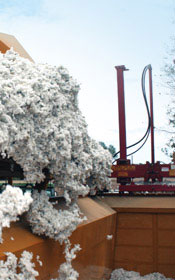
Advancements such as these have aided efficiency at the field level. Farmers now use wider harvesters that handle six to eight rows and employ carts known as boll buggies, which collect the cotton from the harvester and return it to the module builders. This process allows the pickers to spend 70% of the time on the row harvesting.
Some of the newest machines from Case IH and John Deere both pick the cotton and form the modules on the harvester. John Deere’s version even triple-wraps the picked cotton in plastic before the round bales roll off the machine and onto the field.
Innovations such as the module builder and the ongoing work in optimizing the flow between field and gin have advanced cotton’s sustainability by mitigating crop loss, reducing fuel use and fostering an efficient flow of fiber from the field through the gin.
From Efficiency to Sustainability
In the past 10 years, sustainability has become a key word across most industries. Yet Cotton Incorporated was practicing sustainability before it even had a name.
Still, the company knew it was essential that its data be credible and aligned along industry standards. To that end, Cotton Incorporated participates in a number of sustainability initiatives, including Field to Market: The Alliance for Sustainable Agriculture, a consortium of food companies, commodities, brands and retailers focused on reducing the impact of farming and making agriculture more environmentally friendly.
Early on, Cotton Incorporated recognized that reducing pesticide use was a priority because it presented both an economic and environmental cost to growers. Likewise, the company supported research into more efficient water use by producers.
Today, cotton production is highly efficient as a result of modern seed technology, conservation tillage practices, advanced scientific research, and machinery and equipment practices. All have combined to help U.S. farmers increase yield—two times more today than in the 1960s—on the same amount of cotton acreage. In fact, cotton is meeting 30% of the world’s textile needs on 2.5% of agricultural land resources. Future fiber demand can be met on fixed land resources on the expectation of continued yield increase.
Field to Market released an independent research report that shows some impressive advances in the way cotton is grown. According to the Field to Market survey, the environmental impact of producing a pound of cotton in the United States has fallen substantially over the past three decades:
30%
Improvement in land use efficiency
68%
Drop in soil loss
75%
Decline in irrigation water use
31%
Reduction in energy use
22%
Decrease in greenhouse gas (GHG) emissions
Boll Weevil Eradication
These extensive efforts
have resulted in the near total eradication of the boll weevil
throughout the cotton-growing states in America.
In the early days of Cotton Incorporated, the company’s scientists were adamant in combating the threat of the boll weevil. To understand their determination, it is important to note how devastating the insect was both to the environment and to the grower’s bottom line.
The Anthonomus grandis (boll weevil) migrated from Mexico to the United States in the late 1800s and spread rapidly throughout the Cotton Belt. It was the single most destructive pest to the U.S. cotton industry, eventually costing producers more than $15 billion, both from yield losses and costs to control the insect.
In 1958, the National Cotton Council recognized the severity of the boll weevil’s damage, and, with congressional leadership and support, the USDA Boll Weevil Research Lab was created. Eradication experiments and control programs were soon rolled out. In the late 1970s, the National Boll Weevil Eradication Program was launched along the Virginia–North Carolina border. The program soon expanded into other Southeastern states, followed by areas of Arizona, California and Mexico. Later programs were launched in Oklahoma, New Mexico, the Mid-South and Texas.
Cotton Incorporated was unequivocal in the need for grower commitment to the program, and its influence helped engage grower participation.
The eradication involved using three main techniques over a three-to-five-year period: the laying of pheromone traps to detect the presence of the boll weevils, reducing the weevil’s food supply and malathion applications. In its early days, all three techniques were employed in a tiered system. Today, it is much more sophisticated, using GPS mapping and bar-coded traps that can transmit data electronically.
These extensive efforts have resulted in the near-total eradication of the boll weevil throughout cotton-growing states in America. Today, the boll weevil has been eradicated in Virginia, North Carolina, South Carolina, Georgia, Florida, Alabama, Tennessee, Missouri, Arkansas and Mississippi. The Far West is also boll weevil free in California, Arizona, Oklahoma and New Mexico. In Texas, the pests were found in just three of the 16 eradication zones. Numbers have been reduced substantially in two of the zones and remained stable in the third.
There are numerous ecological benefits of the program; perhaps most significant is a reduced need for pesticide applications. Another advantage is that this allows other insects to survive, including natural predators to the boll weevil.
Introduction of Biotech Cotton
In 2008, 44% of U.S. cotton farms had fields
THAT required no foliar insecticides
That same year, nearly one-third of U.S. cotton acreage required no additional insecticide applications.
As devastating as the boll weevil was to the U.S. cotton industry—and still is to other countries—it was not the only pest to have a significant impact on cotton yield. Producers were also faced with attacks from tobacco budworms, cotton bollworms and pink bollworms. By the mid-1990s, invasions from these pests meant a 4% reduction in yields, or a quarter-billion dollars worth of cotton.
By the 1980s, insects had begun to evolve a tolerance to topically applied synthetic insecticides, just as scientists and environmentalists began to realize that improper use of synthetic chemicals had negative impacts on the environment and more benign options were needed.
After years of laboratory research and field trials by numerous scientists worldwide, a bacterium known as Bacillus thuringiensis, or Bt, which is harmless to animals and humans, was successfully incorporated into the DNA of the cotton plant.
Scientists knew Bt was a good candidate for biotech cotton because it had been used as an organic pesticide since 1920, primarily to kill flour moths, without any harmful effects to humans or the environment. Today, Bt is still approved for and widely used in organic farming.
As a liquid spray, Bt was not very effective for insect control because it was negatively affected by the weather: rain rapidly washed it away, and the sun degenerated its beneficial properties. Plants that expressed the Bt protein, however, did not need to be sprayed with chemical insecticides; pests that ate the plant either died or left the field in search of other sources of food.
Cotton Incorporated sponsored research at leading research universities, including Texas A&M and Texas Tech, to expedite a viable, bioengineered Bt protein, and, in 1996, commercial Bt cotton varieties became available to U.S. growers.
Prior to commercialization, the USEPA, the USDA and the FDA subjected Bt cotton, like every other biotech product, to rigorous regulatory evaluation. Comprehensive environmental and human safety studies were conducted, ruling out the possibility of harm to existing plants, nontarget organisms and humans.
From 1996 to 2007, 23% less insecticide active ingredient was used in Bt-adopting countries, and the resulting environmental impact from reduced insecticide use has fallen by 28%, as measured by the Environmental Impact Quotient (EIQ). Since the introduction of Bt cotton, the number of insecticide applications in the United States has been reduced by half. In 2008, 44% of U.S. cotton farms had fields that required no foliar insecticides. That same year, nearly one-third of U.S. cotton acreage required no additional insecticide applications.
Not only has Bt cotton reduced insecticide use, but it has also improved lint yield and reduced the costs to growers, who in turn spend less on insecticide supplies, equipment and labor. Additionally, Bt cotton has lowered the quantity of chemicals that enter the environment. Moving forward, the industry seeks to develop plants that are resistant to an even wider variety of insect pests.
Bt cotton has also
Lowered the quantity of chemicals
that enter the environment
Advances in Pesticides
The global cotton industry accounts for 6.24% of worldwide pesticide sales,
14% of which are insecticides. Fruits and vegetables account for 29%, and cereal crops, such as rice and corn, account for 35%.
Cotton Incorporated’s Agricultural & Environmental Research Division continues to work with scientists and universities to reduce the use of pesticides.
Today, U.S. growers make 50% fewer pesticide applications than the generation before them, primarily because of the introduction of Bt cotton. According to data from Cropnosis, an independent company that monitors agrochemical sales around the world, the global cotton industry accounts for 6.24% of worldwide pesticide sales, 14% of which are insecticides. Fruits and vegetables account for 29%, and cereal crops, such as rice and corn, account for 35%. Consumers need not worry that there may be pesticide residues on their apparel or home goods. Cotton plants are most vulnerable to pests during the early growth stages, which means growers do not need to apply pesticides after the boll opens. In fact, since 1991, the Bremen Cotton Exchange has regularly tested raw cotton fiber from around the world for more than 200 toxic substances, including heavy metals and pesticides. U.S. cotton samples consistently receive an “n.d.” (“not detected”) designation. From a chemical residue standpoint, conventional raw U.S. cotton fiber is no different from organic cotton and satisfies OEKO-TEX® standards.
Advances in Irrigation
64% of U.S. cotton is grown with naturally occurring rainfall.
Globally, cotton uses just 3% of the world’s agricultural water.
Cotton Incorporated is dedicated to preserving our planet’s most valuable natural resource: water. It has taken steps to conserve water usage in both the growing and manufacturing phases.
Cotton is quite drought tolerant; 64% of U.S. cotton is grown with naturally occurring rainfall. Globally, cotton uses just 3% of the world’s agricultural water.
In the United States, irrigation is mainly used to supplement rainfall during dry periods. Cotton Incorporated continues to develop more accurate ways to determine and deliver water to meet crop water needs when those dry periods do occur.
A number of methods are used to water cotton, including surface irrigation and sprinkler systems. One highly desirable delivery method is subsurface drip irrigation (SDI), which delivers water below the soil surface, thereby reducing evaporation. Studies have also shown that cotton grown using SDI watering methods had the highest water use efficiency for lint production.
Research also continues in finding ways to reduce water through effective measurement systems. One such system is the biologically identified optimal temperature interactive console (BIOTIC), developed by the scientists at the USDA ARS. The system provides irrigation scheduling based on measurement of canopy temperatures and the optimal temperature of a given crop species.
Sequencing the Cotton Genome
Cotton Incorporated played an important role in facilitating the mapping of the cotton genome,
an achievement that will greatly accelerate advancements in cotton genetics.
Cotton Incorporated played an important role in facilitating the mapping of the cotton genome, an achievement that will greatly accelerate advancements in cotton genetics.
Both conventional breeders and geneticists believe this discovery will cut development time in half, thus expediting the availability of improved varieties of cotton, whether through genetic modification or conventional breeding. Cotton’s genome sequencing stands as a toolbox for all cotton breeders, those who are breeding conventionally in a green house and geneticists in a lab.
It was more than a decade ago that cotton researchers discussed determining the appropriate path to sequence the genomes of Gossypium, the cotton genus. The community, through the International Cotton Genome Initiative, held open dialogue and ultimately determined the best route was first to sequence the diploid progenitor ancestors of Upland cotton.
While scientists from 31 institutions around the world were working on individual projects, Cotton Incorporated became extremely active in corralling and focusing this research, in addition to providing funding. In 2012, this consortium of scientists successfully mapped the two parent varieties of Upland cotton, the results of which were published in Nature.
The gold standard Gossypium raimondii genome sequence provides the reference blueprint that will revolutionize cotton genetic improvement over the next five to 10 years.
Investment in Sustainability
Cotton Incorporated research and development, though, goes well beyond cotton fiber. The company is also exploring uses for the entire cotton plant in commercially viable, if unexpected, products.
Hydromulch
Though cotton is well known as an apparel and home goods textile fiber, it is increasingly being used in novel, yet beneficial and sustainable, applications. One such case is spray hydromulch, made from by-products of the ginning process.
The cotton ginning process creates 2.5 million tons of biomass each year; spray mulches turn this waste into a practical product that benefits the environment. The deep green hydromulches are hydraulically applied. And since cotton is by nature porous, absorbent and biodegradable, it absorbs adequate amounts of moisture and provides that moisture to vegetation so that it can establish quickly, and erosion from heavy wind and rain is controlled.
Cotton Incorporated collaborated with the USDA’s ARS and Mulch & Seed Innovations of Centre, AL, to develop two all-natural cotton-fiber mulch products that help control soil erosion until grass or other vegetation can take root. The GeoSkinTM cotton hydromulch is ideal for level construction zones, while HydraCX2® is optimal for steep roadside projects.
The ARS tested the cotton hydromulches against commercial erosion control blankets made of wood, paper and synthetics. The results showed the cotton products performed better in preventing runoff and required significantly less labor.
Both products are marketed with the highly recognized Seal of Cotton and have effectively established other revenue sources for cotton.
Biodegradable Packing Material
Cotton Incorporated also collaborated with Ecovative Design, a sustainable material science company, to create Mushroom® Materials—naturally grown, 100% bio-degradable packaging made from cotton by-products. The high-performance packaging can be molded like synthetic foam and is cost competitive and environmentally responsible since it can be composted after usage.
Ecovative produces two packaging materials, Myco Foam and Myco Board. Their low-energy manufacturing process starts with agricultural waste, including cotton burrs, from crop production. This substrate is cleaned and combined with a mushroom component called mycelium, which is the fine white filament produced during the vegetative growth stage of fungi.
The mycelium strands intertwine and reach out toward the substrates. They break down the tough compounds and form a matrix. Ecovative refers to this as a mushroom material. That material is broken up then packed and sealed into molds, in which the material takes on their form.
It is currently being used by a number of companies, from Dell, for their sensitive hard drives, to Puma, for their limited edition stand-up paddle boards. Ecovative recently partnered with Sealed Air Corp., a global packaging solutions leader, to bring the product to customers around the world.
Sustainable Wall Covering
Just as cotton has the ability to absorb water, so too can it absorb heat and sound, which made it the ideal main component in the sustainable wall finish from JaDecor Natural Wallcovering.
The JaDecor product is used in both residential and commercial applications for its ability to decrease everyday noises, such as those from planes or barking dogs, as well as its capacity to promote fuller sound in concert halls.
When Chicago-based testing facility Riverbank Acoustical Laboratories tested JaDecor’s sound absorbency properties using the reverberation room method, it was assigned an impressive 0.15 noise reduction coefficient (NRC).
JaDecor also works as a thermal insulation, providing warmth to interior spaces. The product is made from a mixture of natural cotton fibers and minerals. It is not sold at retail and must be hand-troweled onto walls by a certified installer.
JaDecor is environmentally safe and has a low carbon footprint since it is sourced from U.S. cotton.