The Spindle-Type Cotton Harvester
Maximizing Harvester Capacity & Productivity
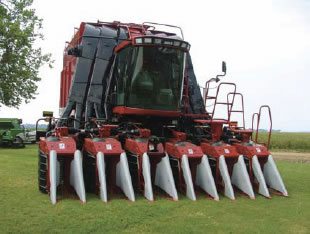
Spindle damage to stalks is about equal, indicating good synchronization of ground speed and the bars/ spindles.
Cotton budgets suggest harvesting expenses are about 16% of crop production costs in the spindle-picked regions of the U.S. In other words, harvesting will cost you about $110 per acre, which equals cost of fertilizer and seed and associated technology fees. Proper management decisions can dramatically influence these costs. Following are several steps to help you reduce harvesting costs:
- Spread the principal and interest costs over more acres by operating more hours per season.
- Increase the capacity (field efficiency) of your harvester operation to gain more actual picking time.
- Arrange field layout to obtain longer rows.
- Arrange field layout to have row end turning distances that will allow you to resume picking quickly after turning.
- Alternatively, you can plant across row ends and then shred stalks to provide a turn space for the field harvest.
- Arrange operations so that the picker turns from longer to shorter rows where rows intersect the turn row at an angle.
- Minimize picker road travel with deliberate plans for field and crop selection and management practices.
- Minimize harvest downtime with improved service and maintenance procedures.
- Provide proper support equipment to obtain minimum unloading times.
- Improve operator skills through training programs and field “coaching.”
- Choose row patterns to obtain a wider harvester swath without lowering yields. For example, use 38-inch rows instead of 30-inch rows or use skip-row planting instead of solid planting (Buehring, et al.).
Picker Drum Arrangements
A 1946 diagram used to explain how an opposed-drum cotton picker works.
All pickers manufactured in the U.S. have two drums in a tandem or staggered, opposed drum arrangement. Early research during spindle-picker development compared drum positions on the same side of the row (in-line) and on opposite sides of the row (opposed drum), as well as different numbers of spindles per bar and bars per drum with a variety of plant sizes and cotton conditions. The front drum of the row unit harvests about 75% of the cotton. Current production pickers have a top-to-bottom spindle contact area of about 30 inches using 18 or 20 spindles per bar. Spindles are spaced 1.625 inches along the bar. Bar cams and cam tracks cause spindles to enter a cotton row pointed slightly toward the rear of the picker and quickly swing to aim slightly forward as they retreat from a row. Bar travel must synchronize with ground speed, causing the spindles’ motion relative to the stalk to be “into” and “out of” the row. When bars are not synchronized with ground travel, spindles typically cause damage on the front or rear of the stalks. Incorrect picker tire size, belt slippage of belt-driven picker units, improper picker adjustment, and incorrectly assembled row-unit drive components are some reasons bars do not synchronize. These situations will result in harvest of trashy seed cotton and excessive power and wear to the row units.
Opposed Drums
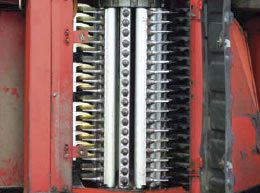
The first cotton pickers introduced had row units with two drums – one on each side of the row. Cotton production at that time had been standardized to 38- to 40-inch rows. So the row units were designed without much consideration of width, other than to prevent the sides from interfering with adjacent rows. The rear drum was generally located just behind the front drum so that the bars of spindles did not interfere. However, length (weight) of the row unit was as short as possible (close to the tractor or carrier).
In the current design, row units are lengthened to allow them to nest and provide a minimum row spacing of about 28-30 inches. These machines have left- and right-handed bars, cam tracks, spindles, and spindle nuts, which increases the number of different parts required to repair a row unit. This design can also cause confusion, leading to spindles being placed in the wrong spindle nut and bar. Such a mistake would cause the spindle to turn in the wrong direction to wrap cotton and then be doffed. Wrong-handed spindles installed in a row unit will wear out doffer and moistening pads and will not pick cotton. The advantage of opposed drum-row units is that they pick from both sides of the plant and will pick a slightly greater percentage of the cotton from the stalk in some field conditions.
In-Line Drums
In-line row unit with both drums on the same side of the row.
15-inch dual row units in a modified skip-row pattern.
In-line drum arrangements have both drums on the right side of the row and only pick from that side of the plant. These units have all right-handed bars, spindles, spindle nuts, and cam tracks for front and rear drums. This arrangement is an advantage for the manufacturer and the producer in parts stocking and assembly.
VRS Row Units
Variable-Row-Spacing (VRS) pickers have the capability to harvest narrower rows (15-inch rows and skip-row planting patterns). A cutter mechanism ahead and to the right of the front picker drum cuts and feeds unpicked stalks into the uncut adjacent row. Plants in the left row remain uncut and are picked in the normal fashion with in-line drums. When skips occur in the uncut row, modified ribs on these front drums and feeder fingers between the drums help move cut stalks through this row unit.
This VRS design is a picker option for cotton growers with lower-yielding soils where narrow-row production is more economical or for growers who use certain skip-row patterns with 15-inch row spacing. This design allows the row units to be spaced wider apart and achieve a 45-inch (two planted, one skipped 15-inch drills) or 60-inch (two planted, two skipped 15-inch drills) effective picking width per row unit. Research has shown that these row patterns yield about the same amount of cotton as conventionally planted 15-inch, 30-inch, and 38- to 40-inch plantings. (See Buehring, et al., “Nonirrigated Spindle Picker 15-Inch and Wide-Row Cotton Production Systems Analysis.”)